Yokogawa Electric Corporation (TOKYO : 6841) et JSR Corporation (JSR, TOKYO : 4185) annonce la conclusion réussie d’un test de terrain dans le cadre duquel l’IA a été utilisée pour faire fonctionner de manière autonome une usine chimique pendant 35 jours, une première mondiale*1. Ce test a confirmé que l’IA basée sur l’apprentissage par renforcement pouvait être appliquée en toute sécurité au sein d’une usine réelle, et a prouvé que cette technologie pouvait contrôler des opérations au-delà des capacités des méthodes de contrôle existantes (contrôle PID*2/contrôle de processus avancé*3), qui nécessitaient jusqu’à présent l’exploitation manuelle des vannes de commande selon l’avis du personnel de l’usine. L’initiative décrite aux présentes a été sélectionnée dans le cadre du programme de subvention des Projets 2020 pour la promotion de la sécurité industrielle avancée, du ministère japonais de l’Économie, du Commerce et de l’Industrie.
Ce communiqué de presse contient des éléments multimédias. Voir le communiqué complet ici : https://www.businesswire.com/news/home/20220321005005/fr/
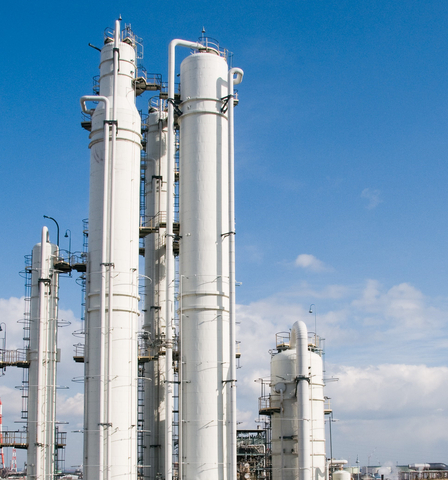
Distillation columns at the JSR chemical plant (Photo: JSR Corporation)
Le contrôle dans le cadre des industries de traitement couvre une large gamme de domaines, qu’il s’agisse du raffinage du pétrole, des produits pétrochimiques, des produits chimiques haute performance, des fibres, de l’acier, des produits pharmaceutiques, des produits alimentaires, ou de l’eau. Tout ceci implique des réactions chimiques et d’autres éléments exigeant un niveau de fiabilité extrêmement élevé.
Concernant ce test de terrain, la solution d’IA a fait face avec succès aux conditions complexes requises pour assurer la qualité des produits et maintenir les liquides dans la colonne de distillation, à un niveau approprié, tout en utilisant au maximum la chaleur résiduelle en tant que source de chaleur. Ce faisant, il a été possible de stabiliser la qualité, d’atteindre un rendement élevé*4, et d’économiser de l’énergie. Tandis que la pluie, la neige et d’autres conditions météorologiques constituaient des facteurs importants susceptibles de perturber l’état de contrôle en causant des changements soudains de la température atmosphérique, les produits qui ont été fabriqués ont satisfait à des normes rigoureuses et ont depuis été expédiés. En outre, dans la mesure où seuls des produits de bonne qualité ont été fabriqués, les pertes en termes de carburant, de main-d’œuvre, de temps, et autres, liées à la fabrication de produits hors spécifications, ont été éliminées. La sécurité des opérations a été assurée grâce à un processus en trois étapes.
L’IA utilisée dans le cadre de cette expérimentation de contrôle, le protocole Factorial Kernel Dynamic Policy Programming (FKDPP), a été développée conjointement par Yokogawa et l’Institut des sciences et technologies de Nara (Nara Institute of Science and Technology, NAIST) en 2018, et a été récompensée lors du Congrès international de l’IEEE sur la science et l’ingénierie de l’automatisation, en tant que première IA basée sur l’apprentissage par renforcement, au monde, et pouvant être utilisée dans le cadre de la gestion des usines*7. À l’issue de plusieurs initiatives telles que la conduite réussie d’une expérimentation portant sur un système de formation de contrôle*8 en 2019, ainsi qu’une expérimentation réalisée en avril 2020 au moyen d’un simulateur pour recréer une usine entière*9, Yokogawa confirme le potentiel de cette IA de contrôle autonome*10, en la faisant passer du statut de théorie à celui de technologie apte à une utilisation pratique. La solution peut être utilisée dans des domaines au sein desquels l’automatisation était jusque-là irréalisable en utilisant les méthodes de contrôle conventionnelles (contrôle PID et contrôle de processus avancé) ; et ses atouts incluent la capacité à gérer des objectifs contradictoires comme peuvent l’être la haute qualité et les économies énergétiques.
Compte tenu des nombreux phénomènes physiques et chimiques complexes ayant un impact sur les opérations en usine, il existe encore de multiples situations où les opérateurs expérimentés doivent intervenir et exercer un contrôle. Même lorsque les opérations sont automatisées à l’aide d’un contrôle PID et un contrôle de processus avancé, des opérateurs hautement expérimentés sont amenés à interrompre le contrôle automatisé, pour modifier la configuration et les valeurs de sortie, par exemple, en cas de changement soudain de la température atmosphérique suite à des précipitations ou d’autres événements météorologiques. Il s’agit d’un problème courant dans les usines de nombreuses entreprises. En ce qui concerne la transition vers une autonomie industrielle*11, la mise en place d’un contrôle autonome dans les situations où jusqu’à présent une intervention manuelle était essentielle, et ce, avec le moins d’effort possible tout en garantissant un haut niveau de sécurité, a été particulièrement complexe. Les résultats de ce test suggèrent que la collaboration entre Yokogawa et JSR a ouvert la voie à la résolution de cette problématique de longue date.
Yokogawa invite les clients intéressés à participer à ce type d’initiatives à travers le monde. La société entend fournir rapidement des produits et solutions qui conduisent à la concrétisation de l’autonomie industrielle.
JSR considère que cette démonstration souligne le potentiel de l’IA à relever des défis jusque-là impossibles à résoudre dans les usines chimiques, et étudiera son application à d’autres processus et usines, en vue d’améliorer encore davantage la productivité.
À l’avenir, les deux entreprises continueront de collaborer et d’étudier de nouveaux moyens d’utiliser l’IA au sein des usines.
Masataka Masutani, directeur général des technologies de production chez JSR, a commenté : « Dans un environnement en pleine évolution, soumis à divers facteurs tels que l’introduction complète de la 5G et d’autres développements en direction d’une société numérique, ajoutés au vieillissement des ressources humaines chargées d’assurer la sécurité des usines, et au manque de ressources humaines pour les remplacer, l’industrie pétrochimique subit une forte pression pour améliorer la sécurité et l’efficience dans ses activités de production, au moyen de nouvelles technologies comme l’IdO et l’IA. JSR entend rendre la production intelligente grâce à l’intégration proactive des drones, capteurs IdO, caméras, et autres technologies d’avant-garde ; et dans le cadre de cette expérimentation, nous avons relevé le défi de l’automatisation du contrôle des processus d’usine, en utilisant des technologies de contrôle basées sur l’IA. Après avoir vérifié que l’IA était apte à contrôler de manière autonome les processus jusque-là exécutés manuellement selon l’expérience des opérateurs, nous sommes profondément convaincus de l’utilité et du potentiel futur du contrôle basé sur l’IA. D’après les personnes présentes sur le terrain, nous avons entendu des commentaires selon lesquels non seulement la charge pesant sur les opérateurs était réduite, mais le simple fait d’avoir relevé avec succès le défi de cette nouvelle technologie fournissait une motivation pour faire avancer la transformation numérique vers l’avenir. Désormais, nous développerons les opérations contrôlées par l’IA, en nous attachant à améliorer la sécurité, la stabilité et la compétitivité des usines chimiques. »
Takamitsu Matsubara, professeur agrégé au NAIST, a souligné pour sa part : « Je suis très heureux d’apprendre que ce test sur le terrain a été un succès. Bien que les analyses de données et l’apprentissage automatique soient désormais appliqués aux opérations d’usines chimiques, la technologie utilisée dans le cadre du contrôle autonome et de l’optimisation des opérations n’est pas encore totalement au point. L’algorithme FKDPP d’IA basée sur l’apprentissage par renforcement a été conjointement développé par Yokogawa et le NAIST en 2018, afin de mettre en œuvre le contrôle autonome dans les usines chimiques. Malgré la nécessité de recourir à un grand nombre de capteurs et de vannes de commande, l’IA peut générer une politique de contrôle robuste dans le cadre d’un nombre limité d’essais d’apprentissage. Ces fonctionnalités ont contribué à améliorer l’efficience du processus de développement, et ont conduit à la réalisation d’un contrôle autonome pendant une longue période de 840 heures lors du test effectué sur le terrain. Je suis convaincu que cette réalisation difficile d’un contrôle autonome dans une colonne de distillation réelle, ajoutée au fait que le niveau d’application pratique a été rehaussé de manière à ce que l’ensemble du processus de production et de la sécurité soient intégrés dans un seul système, revêt une importance majeure pour l’ensemble du secteur. J’ai hâte de voir les progrès que nous réserve cette technologie. »
Kenji Hasegawa, vice-président de Yokogawa Electric et directeur de la division des Produits, chez Yokogawa, a ajouté : « Le succès de ce test de terrain résulte de la combinaison entre les connaissances approfondies du processus de production, et les aspects opérationnels que seul le client peut fournir, complétée par la puissance de Yokogawa, consistant à tirer parti des mesures, du contrôle et des informations, pour produire de la valeur. Ce test suggère que l’IA de contrôle autonome (FKDPP) peut grandement contribuer à l’automatisation de la production, à la maximisation du RSI, ainsi qu’à la durabilité environnementale à travers le monde. Yokogawa a joué un rôle de chef de file mondial dans le développement de systèmes de contrôle distribués qui contrôlent et surveillent l’exploitation des usines de production, soutenant ainsi la croissance dans tout un éventail de secteurs d’activités. Gardant les yeux rivés sur un monde où l’exploitation autonome façonne le modèle du futur des industries, nous promouvons désormais le concept d’IA2IA désignant l’Automatisation industrielle destinée à l’autonomie industrielle (Industrial Automation to Industrial Autonomy). Pour assurer une production solide et flexible qui prenne en considération l’impact des différences parmi les hommes, les machines, les matériaux et les méthodes, les 4M, dans les secteurs de l’énergie, des matériaux, des produits pharmaceutiques et bien d’autres, nous entendons accélérer le développement conjoint de l’IA de contrôle autonome, aux côtés de nos clients à travers le monde. »
*1 |
Selon un sondage de Yokogawa Electric, mené en février 2022, concernant l’IA qui modifie directement la variable de manipulation dans les usines chimiques. |
*2 |
Contrôle proportionnel, intégral, dérivé. Initialement proposé par Nicolas Minorsky en 1922, il s’agit d’une technologie de contrôle des infrastructures, destinée aux industries de traitement, et utilisée pour contrôler divers éléments tels que la quantité, la température, le niveau, la pression et les ingrédients. Elle applique un contrôle sur une valeur cible, tout en utilisant les résultats de chacun des calculs P, I et D, en fonction de l’écart entre la valeur actuelle et la valeur programmée. Ce mode de contrôle implique plusieurs problématiques, notamment l’incapacité à gérer de multiples perturbations externes (changements météorologiques, climatiques, de composition des matériaux), et le changement fréquent des valeurs cibles, d’où la nécessité d’un contrôle manuel. |
*3 |
Contrôle de processus avancé. Cette méthode utilise un modèle mathématique capable de prédire les réponses des processus, et fournit en temps réel des valeurs programmées à la boucle de contrôle PID, afin d’améliorer la productivité, la qualité et la contrôlabilité. En outre, elle s’applique facilement au contrôle dans le but d’augmenter la production, de réduire le temps de travail, et d’économiser de l’énergie. L’intégration des résultats du contrôle de processus avancé entraînant des écarts plus faibles dans les données, il est possible de se rapprocher des limites de performance opérationnelle (c’est à dire, l’état dans lequel la performance optimale peut être atteinte). Il s’agit toutefois d’une méthode limitée, dans la mesure où elle n’est pas capable de réagir à la vaporisation rapide des fluides, et à d’autres réactions chimiques, ni aux changements majeurs dans la composition des matériaux, et aux modifications au niveau des machines. |
*4 |
Le volume de substance cible qui est effectivement obtenu à partir des matières premières via un processus de raffinage |
*5 |
Le système de contrôle intégré CENTUM VP permet à l’ensemble du processus de production de fonctionner, tout en surveillant et en contrôlant les pressions, les débits, les températures et d’autres facteurs de ce type, avec plusieurs fonctions de verrouillage pour une exploitation sécurisée et stable où les accidents peuvent ainsi être évités. Afin de prévenir les accidents d’usine, il est possible de faire fonctionner le système conjointement à des Systèmes instrumentés de sécurité (SIS), des Dispositifs d’arrêt d’urgence (DAU), des Systèmes de sécurité incendie (SSI), etc. |
*6 |
Mécanisme qui empêche le démarrage, à moins que certaines conditions ne soient remplies avant la mise en service. Il augmente la sécurité en empêchant les opérations incorrectes, les erreurs de procédure, etc. |
*7 |
Factorial Kernel Dynamic Policy Programming for Vinyl Acetate Monomer Plant Model Control, août 2018. https://ieeexplore.ieee.org/document/8560593/ Institut des ingénieurs électriciens et électroniciens (Institute of Electrical and Electronics Engineers, IEEE). L’IEEE est une organisation de recherche académique et de normalisation technique, basée aux États-Unis, et spécialisée dans les domaines du génie électrique et du génie des technologies de l’information. L’Institut compte plus de 400 000 membres dans 160 pays à travers le monde. |
*8 |
Système de contrôle de niveau à trois réservoirs, utilisé à des fins expérimentales et de formation, impliquant la régulation du débit d’eau d’un niveau à l’autre, dans le but de maintenir le niveau d’eau à sa valeur la plus faible. Il inclut également des dispositifs permettant de créer artificiellement des perturbations qui modifient le débit d’eau de manière aléatoire. Compte tenu de la nature des fluides, le contrôle de leurs débits représente un défi de taille pour les industries de traitement. La possibilité d’effectuer un tel contrôle de manière adéquate entraîne une productivité accrue au sein des sites de fabrication. |
*9 |
Scalable Reinforcement Learning for Plant-wide Control of Vinyl Acetate Monomer Process, Control Engineering Practice, Volume 97, avril 2020 https://www.sciencedirect.com/science/article/pii/S0967066120300186 |
*10 |
Yokogawa définit l’IA de contrôle autonome comme une IA qui déduit de manière indépendante la méthode de contrôle optimale, et possède un haut niveau de robustesse lui permettant de gérer de manière autonome, dans une certaine mesure, des situations qu’elle n’a jamais rencontrées auparavant. |
*11 |
L’autonomie industrielle est définie par Yokogawa comme suit : « Les actifs et opérations d’usine possèdent des capacités adaptatives d’apprentissage, permettant d’assurer leur fonctionnement avec une interaction humaine minimale, ce qui donne aux opérateurs les moyens d’effectuer des tâches d’optimisation de niveau supérieur. » Dans les réponses fournies dans le cadre du Sondage mondial des utilisateurs finaux, sur la mise en œuvre de l’autonomie industrielle, mené par Yokogawa en 2021 et impliquant 534 décideurs au sein de 390 entreprises de fabrication, 42 % ont déclaré que l’application de l’IA pour l’optimisation des processus d’usine aurait un impact considérable sur l’autonomie industrielle au cours des trois prochaines années. |
|
(Référence : https://web-material3.yokogawa.com/1/30261/tabs/The_Acceleration_of_Industrial_Autonomy_English.pdf) |
Les noms des sociétés, organisations, produits, services, et logos mentionnés dans ce communiqué sont des marques commerciales ou des marques déposées de Yokogawa Electric Corporation, de JSR Corporation, ou de leurs détenteurs respectifs. |
À propos de Yokogawa
Yokogawa fournit des solutions avancées dans les domaines de la mesure, du contrôle-commande et de l’information aux clients, dans une multitude de secteurs parmi lesquels l’énergie, les matériaux, les produits chimiques et pharmaceutiques, et l’agroalimentaire. Yokogawa résout les problématiques des clients concernant l’optimisation de la production, des actifs et de la chaîne d’approvisionnement, grâce à l’application efficace de technologies numériques, qui permettent une transition vers des opérations autonomes.
Fondée à Tokyo en 1915, et forte de ses 17 500 employés, dans le cadre d’un réseau de 119 entreprises couvrant 61 pays dans le monde, Yokogawa travaille sans relâche en direction d’une société durable.
Pour en savoir plus, rendez-vous sur www.yokogawa.com
À propos de JSR Corporation
JSR Corporation est une multinationale employant plus de 9 000 personnes à travers le monde, et l’un des principaux fournisseurs de matériaux destinés à divers marchés axés sur la technologie, qui s’attache à stimuler l’innovation autour des matériaux grâce auxquels elle crée de la valeur afin d’enrichir la société, les individus et l’environnement. Basé à Tokyo (au Japon), le réseau mondial de JSR comprend des usines et des bureaux en Europe, aux États-Unis, en Chine, à Taïwan, en Corée, et en Thaïlande. JSR est une organisation axée sur la recherche, qui entretient des collaborations étroites avec des innovateurs de premier plan dans plusieurs secteurs clés pour le bien-être présent et futur de la société humaine : sciences de la vie, matériel électronique, solutions d’affichage, plastiques et caoutchoucs synthétiques.
Pour en savoir plus sur JSR Corporation, rendez-vous sur https://www.jsr.co.jp/jsr_e
Aperçu du test de terrain
1. Objectif du test de terrain
(1) Démontrer que l’IA basée sur l’apprentissage par renforcement (FKDPP : algorithme Factorial Kernel Dynamic Policy Programming) peut être appliquée en toute sécurité dans des usines où la sécurité constitue une nécessité absolue
(2) Démontrer que l’IA basée sur l’apprentissage par renforcement peut être mise à profit pour contrôler des zones où il n’est pas possible d’automatiser en utilisant les méthodes de contrôle existantes (contrôle PID/contrôle de processus avancé)
2. Informations détaillées
Localisation |
|
Zones |
|
IA de contrôle |
|
Produits et technologies
|
Yokogawa :
|
Exploitation |
Permet à l’ensemble du processus de production de fonctionner, tout en surveillant et contrôlant les pressions, les débits, les températures et d’autres facteurs de ce type, avec plusieurs fonctions de verrouillage pour une exploitation sécurisée et stable, où les accidents peuvent être évités. Afin de prévenir les accidents d’usine, le système fonctionne conjointement à des dispositifs d’arrêt d’urgence (DAU), des systèmes de sécurité incendie (SSI), etc. |
Processus de mise en œuvre de l’IA |
Création d’un modèle de contrôle basé sur l’IA, grâce à un simulateur d’usine
Évaluation globale de la validité et de la fiabilité du modèle de contrôle basé sur l’IA
Assurer la sécurité, puis contrôler une véritable usine
|
Période du projet |
|
Période d’exploitation continue |
|
3. Rôle des entreprises
JSR |
|
Yokogawa |
|
4. Résultats et comparaison avec le contrôle conventionnel
Résumé
|
|
Intervention |
|
Qualité |
|
Rendement |
|
Économies |
|
Coût |
|
Pertes de temps |
|
Sécurité |
|
5. [Référence] Principales caractéristiques de l’IA utilisée dans le cadre du contrôle des usines
Type |
Fonctionnalités |
Avantages |
|
Contrôle |
Dans les zones où l’automatisation est irréalisable à l’aide des méthodes de contrôle existantes (contrôle PID/contrôle de processus avancé), l’IA déduit par elle-même la méthode optimale de contrôle, et possède un niveau de robustesse lui permettant de contrôler de manière autonome, dans une certaine mesure, des situations qu’elle n’a jamais rencontrées auparavant. |
Sur la base du modèle de contrôle qu’elle apprend et déduit, l’IA applique le niveau de contrôle requis pour chaque situation. |
Les avantages du FKDPP sont les suivants :
(1) Peut être appliqué dans des situations où le contrôle ne peut être automatisé en utilisant les techniques de contrôle existantes (contrôle PID/contrôle de processus avancé), et peut gérer des objectifs contradictoires, consistant par exemple à assurer une haute qualité tout en réalisant des économies d’énergie. |
Prise en charge des |
L’IA peut prendre en charge la tâche actuellement exécutée par les opérateurs, et consistant à saisir des valeurs cibles dans les zones où l’automatisation a été mise en œuvre en utilisant des méthodes de contrôle traditionnelles (contrôle PID/contrôle de processus avancé). |
L’IA utilise les données de contrôle, antérieures pour effectuer des calculs, et applique les valeurs cibles. |
|
Support opérationnel pour les |
L’IA suggère des valeurs cibles servant de référence pour les opérateurs. |
L’IA exploite les données de contrôle, antérieures pour suggérer à l’homme des valeurs cibles. |
|
Le texte du communiqué issu d’une traduction ne doit d’aucune manière être considéré comme officiel. La seule version du communiqué qui fasse foi est celle du communiqué dans sa langue d’origine. La traduction devra toujours être confrontée au texte source, qui fera jurisprudence.
Consultez la version source sur businesswire.com : https://www.businesswire.com/news/home/20220321005005/fr/